So it’s been a bit of a slow week with regards to posts on my blog, the reason being I have conversely very busy at Hatch knuckling down and helping out. In my last post I mentioned the sheer scale of Hatch’s level of production, between 500-600 designs are handset and printed each year. My experience at Hatch has been the application of my letterpress knowledge to a high speed and high volume print environment. Their mantra is that the “Printer is the designer”, jobs are either faxed or placed in person at the shop and simply consist of the copy needed and perhaps a very rough suggestion of what they want on it (“maybe something with a bird” etc). These are then divided between their team of interns and full time printers, Hatch’s house style is so synonymous with letterpress that having something for your brand/band/family both designed and printed is part of the appeal.
Seeing the everyday workarounds to the problems you encounter when printing remind me of my own experiences when I was regularly screen printing in my studio, you change your tools and space to suit your needs and not the other way round. The layout and work flow of the studio at first is incredibly jarring. For a start though there is a rough organisation to the type cases with regards to size and style there are as many anomalies to this organisation as there are standard placements. Though the drawers are roughly labelled the staff know the layout and it’s peculiarities so well that most of the type setting is done by memory. When printing a run of posters they are are first stacked vertically in small batches on a chair before being leant in these batches against the huge walls of shelves used to store the very large wood type. I will admit at first I was skeptical of this as a drying methods, but the proof was in the process–the chair is the perfect size to enable you to place a print in the current stack with no effort and whilst doing a large run it allows you to really get into the flow of things rather than having to break the motion by moving from the press to a drying rack.
So amongst this many armed, extremely productive beast of lead, iron and wood I have been rummaging through cabinets and helping to set type ready for restrikes (reprints) of original prints from their huge back catalog of designs.
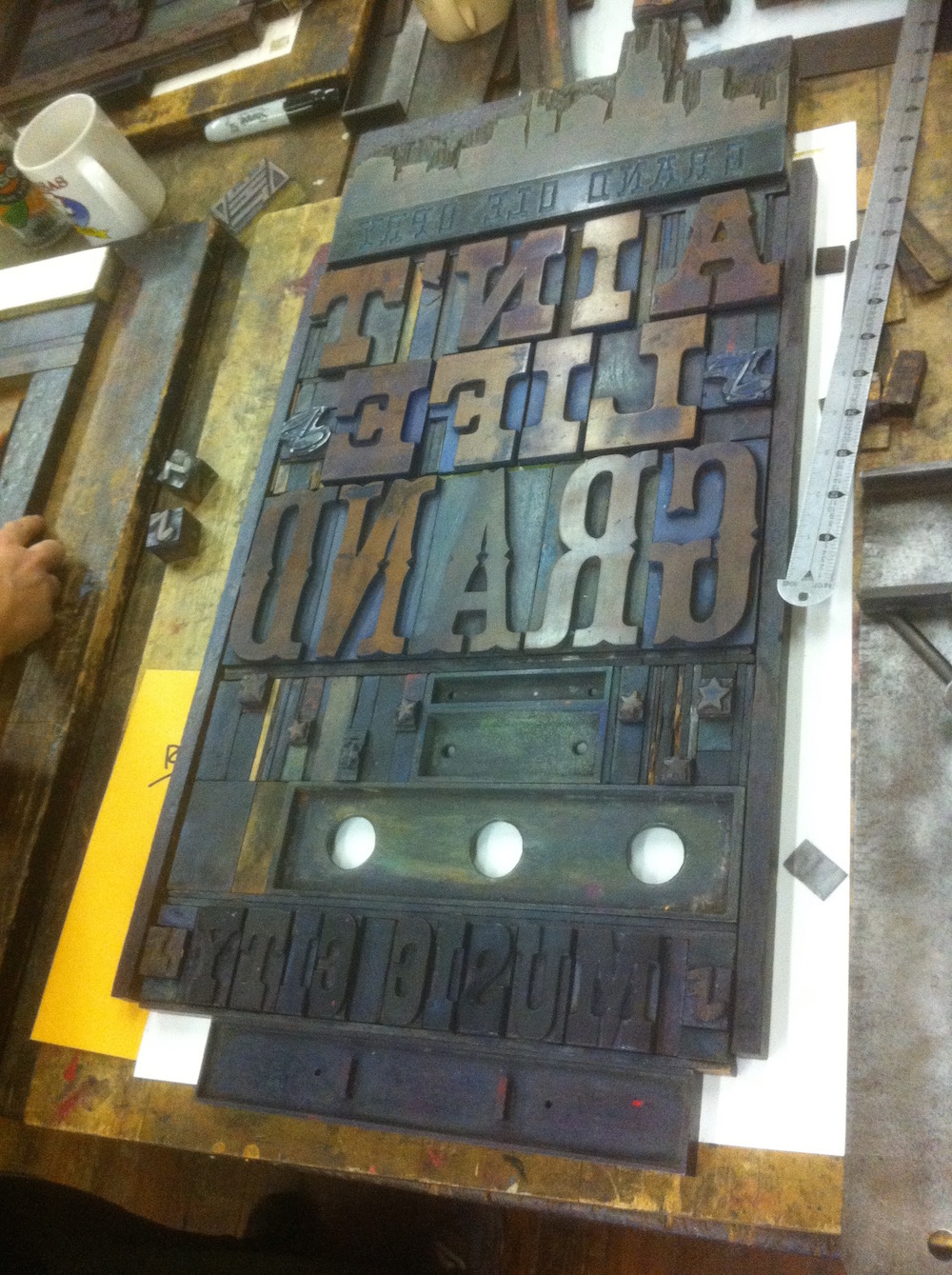